Slot-die Coating with the LP50 – Background and Applications
Welcome to our guide on slot-die coating. Learn the fundamentals, equipment, and tips for precise thin-film deposition. Master this versatile process for uniform coatings on various substrates for a broad variety of applications.
Slot-die coating is a solution-based technology that creates thin films on flat substrates such as metal foils, glass, polymers, paper, and textiles. The liquid is uniformly deposited on the substrate via the slot-die head, which distributes it through a slit-like opening while moving the slot-die relative to the substrate. Slot-die coating can generally be applied in a wide range of industries. Typically, R2R applications are favored in industry due to their high throughput. However, it is fortunate that slot-die coating processes and appropriate materials can be developed without the requirement of an R2R-capable system. Small amounts of materials and substrates can be used with S2S systems for research and development of coatings. With our technology, the LP50 can be transformed into a sheet-to-sheet slot-die coating system.
This enables the development of materials and processes for various applications, some of which we will list below (incl. some references for further reading):
- Batteries and capacitors ([Haw19], [Rey21], [Sch16],[Blo20],[Guo23])
- Thin film solar cells in particular cells based on perovskite materials and organic solar cells ([Li23],[Pat20],[Val23])
- Fuel cells, electrolysis and Power to X (P2X) applications in general ([Cre22],[Sta19])
- OLED devices, printed electronics ([Lee20],[Amr18],[Par16])
- Water purification ([Kim20],[Pem21])
- Food packaging and medical applications ([Sch23],[Pem21])
- Even porous media including paper, textiles, filters, etc. for various applications ([Din17])
Components of a slot die coating system
In order to perform slot-die coating, the necessary components include a fluid reservoir, a pump to transfer the liquid from the reservoir through the slot-die, and equipment to handle the sample and position the slot-die accordingly. It is important to select each component thoughtfully as they all impact the outcome of the coating. The pump and slot-die must align with the liquid’s rheology and the desired coating thickness. The equipment used to position the slot-die in proximity to the sample requires a high level of parallelity between the slot-die and sample, as well as precise motion control that is synchronized with the pump. Any deviation from these conditions will result in reduced reproducibility and film homogeneity issues.
Film processing control
Numerous parameters enable the control of the film deposition process. Upon selecting the slot-die, the slot geometry may be adjusted by utilising various shims, which aid in the alteration of slot height, width, and length.
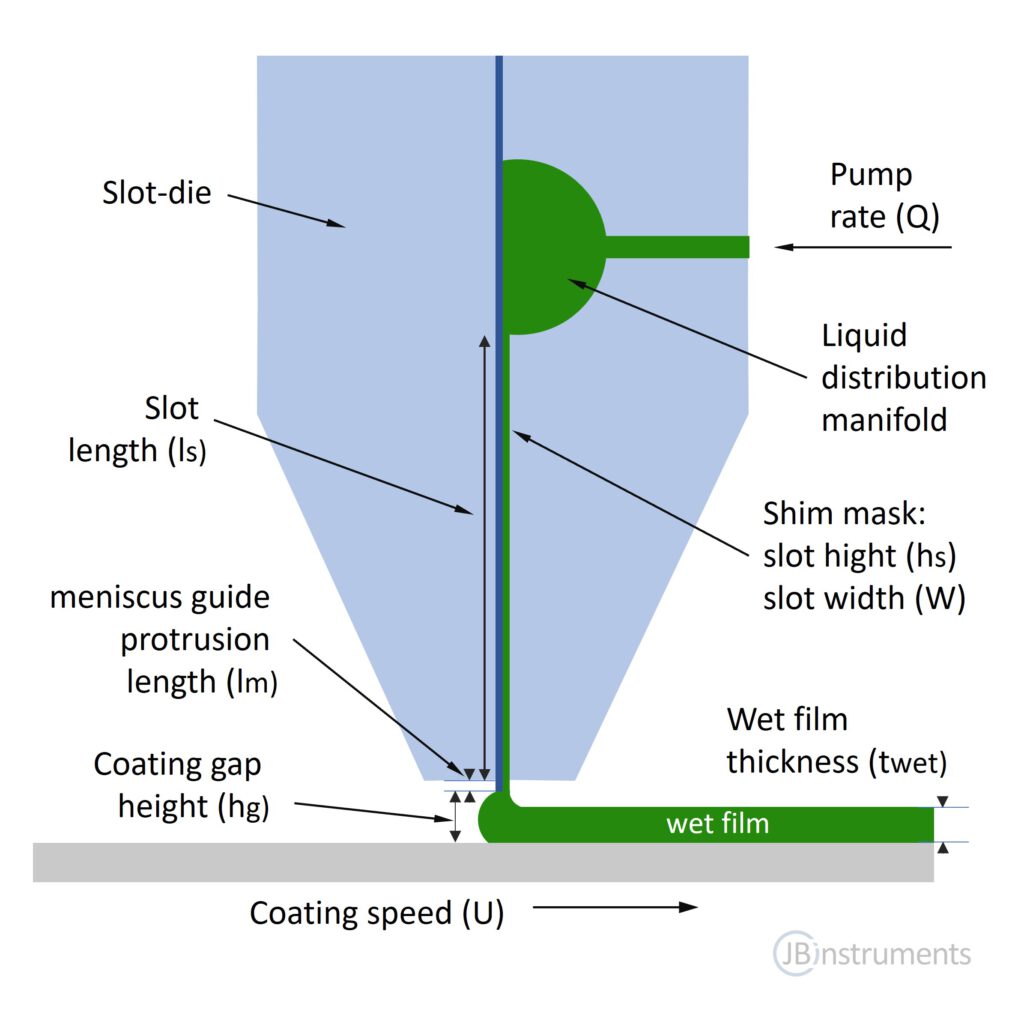
One important property of slot-die coating is its pre-metered nature. The total fluid flow is defined by pump flow rate Q. The resulting wet film thickness twet is a function of Q, the coating speed U and the coating width W: twet=Q/(W*U).
Making sure the slot-die and the substrate table are aligned perfectly
Aligning the slot-die and substrate table can be a challenging task, but it is vital for achieving uniform processing outcomes. The LP50’s inbuilt camera-based optical alignment system simplifies and accelerates this task significantly. Adjusting the slot-die height to accommodate the substrate thickness or amend the coating gap is effortless with the software.
Process development
To obtain uniform coatings, it is crucial to precisely adjust both the geometry and ink formulations to operate the system within the correct processing window. Any deviation from this range will lead to the occurrence of various coating defects. For further reading, we recommend the following publications [Bha11] [Bha13][Din16] [Sch22].
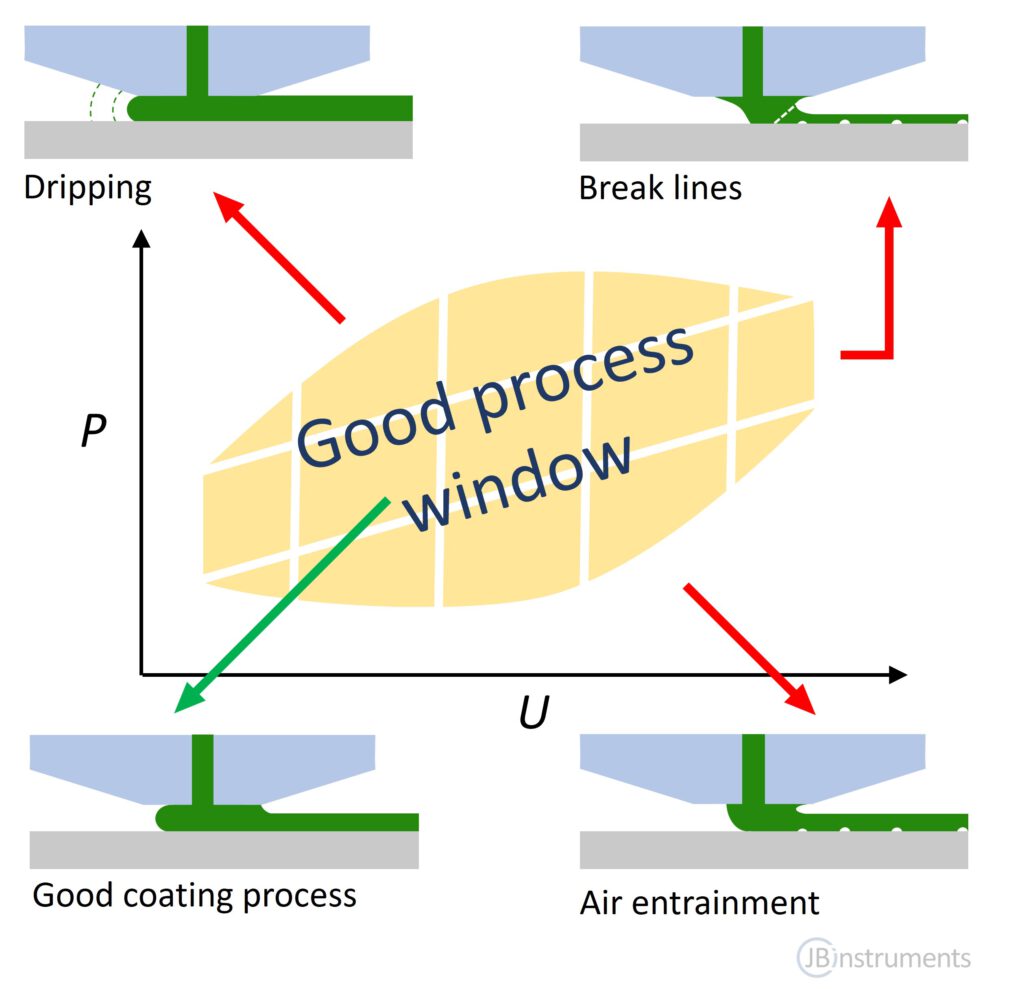
References
[Amr18] Amruth C. et al., Slot-Die Coating of Double Polymer Layers for the Fabrication of Organic Light Emitting Diodes, Micromachines, (2019), 10, 53, https://doi.org/10.3390/mi10010053
[Bha11] Bhamidipati et al., Wetting phenomena during processing of high-viscosity shear-thinning fluid, Journal of Non-Newtonian Fluid Mechanics, Volume 166, Issues 12–13, (2011), Pages 723-733, https://doi.org/10.1016/j.jnnfm.2011.03.009
[Bha13] Bhamidipati et al., Slot die coating of polybenzimiazole based membranes at the air engulfment limit, Journal of Power Sources, Volume 239, (2013), Pages 382-392, https://doi.org/10.1016/j.jpowsour.2013.03.132
[Blo20] Blomquist et al., Influence of Substrate in Roll-to-roll Coated Nanographite Electrodes for Metal-free Supercapacitors, Sci Rep 10, 5282 (2020), https://doi.org/10.1038/s41598-020-62316-0
[Cre22] Creel et al., Slot-die-coating operability windows for polymer electrolyte membrane fuel cell cathode catalyst layers, Journal of Colloid and Interface Science, Volume 610, (2022), Pages 474-485, https://doi.org/10.1016/j.jcis.2021.11.047
[Din16] Ding et al., A review of the operating limits in slot die coating processes, AIChE J., (2016), 62: 2508-2524, https://doi.org/10.1002/aic.15268
[Din17] Ding et al., Review on penetration and transport phenomena in porous media during slot die coating, J. Polym. Sci. Part B: Polym. Phys., (2017), 55, 1669-1680. https://doi.org/10.1002/polb.24307
[Guo23] Guo et al., Large‐Area Smooth Conductive Films Enabled by Scalable Slot‐Die Coating of Ti3C2Tx MXene Aqueous Inks, Advanced Functional Materials, 33.15, (2023), 2213183, https://doi.org/10.1002/adfm.202213183
[Haw19] Hawley et al., Electrode manufacturing for lithium-ion batteries—Analysis of current and next generation processing, Journal of Energy Storage, Volume 25, (2019), 100862, https://doi.org/10.1016/j.est.2019.100862
[Kim20] Kim et al., Scalable fabrication of deoxygenated graphene oxide nanofiltration membrane by continuous slot-die coating, Journal of Membrane Science, Volume 612, (2020), 118454, https://doi.org/10.1016/j.memsci.2020.118454
[Lee20] Lee et al., Increased stripe density of slot-coated PEDOT:PSS using a meniscus guide with linearly tapered μ-tips for OLEDs, Organic Electronics, Volume 83, (2020), 105772, https://doi.org/10.1016/j.orgel.2020.105772
[Li23] Li et al., Current State and Future Perspectives of Printable Organic and Perovskite Solar Cells, Adv. Mater., (2023), 2307161, https://doi.org/10.1002/adma.202307161
[Pat20] Patidar et al., Slot-die coating of perovskite solar cells: An overview, Materials Today Communications, Volume 22, (2020), 100808, https://doi.org/10.1016/j.mtcomm.2019.100808
[Par16] Park et al., Organic thin-film transistors fabricated using a slot-die-coating process and related sensing applications, RSC Adv., (2016), 6, 101613-101621, https://doi.org/10.1039/C6RA18545B
[Pem21] Pemble et al., A Slot-Die Technique for the Preparation of Continuous, High-Area, Chitosan-Based Thin Films, Polymers, (2021), 13, 1566, https://doi.org/10.3390/polym13101566
[Rey21] Reynolds et al., A review of metrology in lithium-ion electrode coating processes, Materials & Design, Volume 209, (2021), 109971, https://doi.org/10.1016/j.matdes.2021.109971
[Sch16] M. Schmitt, Slot die coating of lithium-ion battery electrodes, PhD Thesis, Karlsruhe, Germany, (2016), DOI: 10.5445/KSP/1000051733
[Sch22] P. M. Schweizer, in Premetered Coating Methods: Attractiveness and Limitations (Ed: P. M. Schweizer), Springer International Publishing, Cham, Switzerland, (2022), pp. 511–593, https://doi.org/10.1007/978-3-031-04180-8
[Sch23] Schiessl et al., A Comparative Study on the Roll-to-Roll Processing of a Silicate–Polyvinyl Alcohol Composite Barrier Lacquer Using Slot-Die and Reverse Gravure Coating Techniques, Polymers, (2023), 15, 2761, https://doi.org/10.3390/polym15132761
[Sta19] Stähler et al., A completely slot die coated membrane electrode assembly, International Journal of Hydrogen Energy, Volume 44, Issue 14, (2019), Pages 7053-7058, https://doi.org/10.1016/j.ijhydene.2019.02.016
[Val23] Valsalakumar et al., An Overview of Current Printing Technologies for Large-Scale Perovskite Solar Cell Development, Energies, (2023), 16(1):190, https://doi.org/10.3390/en16010190